Tank Welding Inspection: Making Sure Long-Term Longevity and Safety And Security
Tank Welding Inspection: Making Sure Long-Term Longevity and Safety And Security
Blog Article
The Essential Role of Container Welding Evaluation in Ensuring Structural Stability and Security Conformity in Industrial Applications
In the realm of industrial applications, container welding examination emerges as a pivotal aspect in protecting architectural stability and ensuring conformity with security laws. Using a mix of strategies such as visual analyses and progressed testing techniques, these examinations serve to recognize and mitigate prospective imperfections before they intensify right into significant risks.
Relevance of Tank Welding Evaluation

Guaranteeing compliance with industry criteria and policies is one more considerable facet of container welding examination. Regulative bodies mandate stringent standards for the building and construction and upkeep of storage tanks, and extensive examinations aid companies follow these demands. Non-compliance can result in severe charges, including penalties and shutdowns, further emphasizing the need for strenuous evaluation protocols.
Additionally, container welding examination plays an important function in maintaining functional performance. In summary, the importance of container welding assessment exists in its ability to safeguard public health and wellness, secure the environment, and make sure compliance with governing frameworks.
Secret Examination Strategies
Reliable container welding examination depends on a variety of crucial methods that guarantee thorough assessment of weld quality and architectural stability. Amongst one of the most prevalent methods are aesthetic examination, ultrasonic screening, radiographic testing, and magnetic bit screening - Tank Welding Inspection. Each method provides special benefits in assessing various aspects of the weld
Visual examination works as the first line of defense, enabling assessors to recognize surface area flaws, irregularities, or disparities in the weld bead. Ultrasonic testing utilizes high-frequency audio waves to spot internal imperfections, such as fractures or spaces, providing an extensive evaluation of weld honesty. This approach is specifically reliable in detecting concerns that may not show up externally.
Radiographic testing utilizes X-rays or gamma rays to produce images of the welds, revealing internal gaps and providing a permanent document for future reference. This strategy is extremely effective for vital applications where the risk of failing must be lessened.
Last but not least, magnetic fragment testing is used to determine surface area and near-surface problems in ferromagnetic materials. By using magnetic areas and fine iron bits, examiners can pinpoint discontinuities that may jeopardize the structural stability of the storage tank. With each other, these techniques create a robust structure Check Out Your URL for ensuring top notch welds in industrial applications.
Compliance With Security Specifications
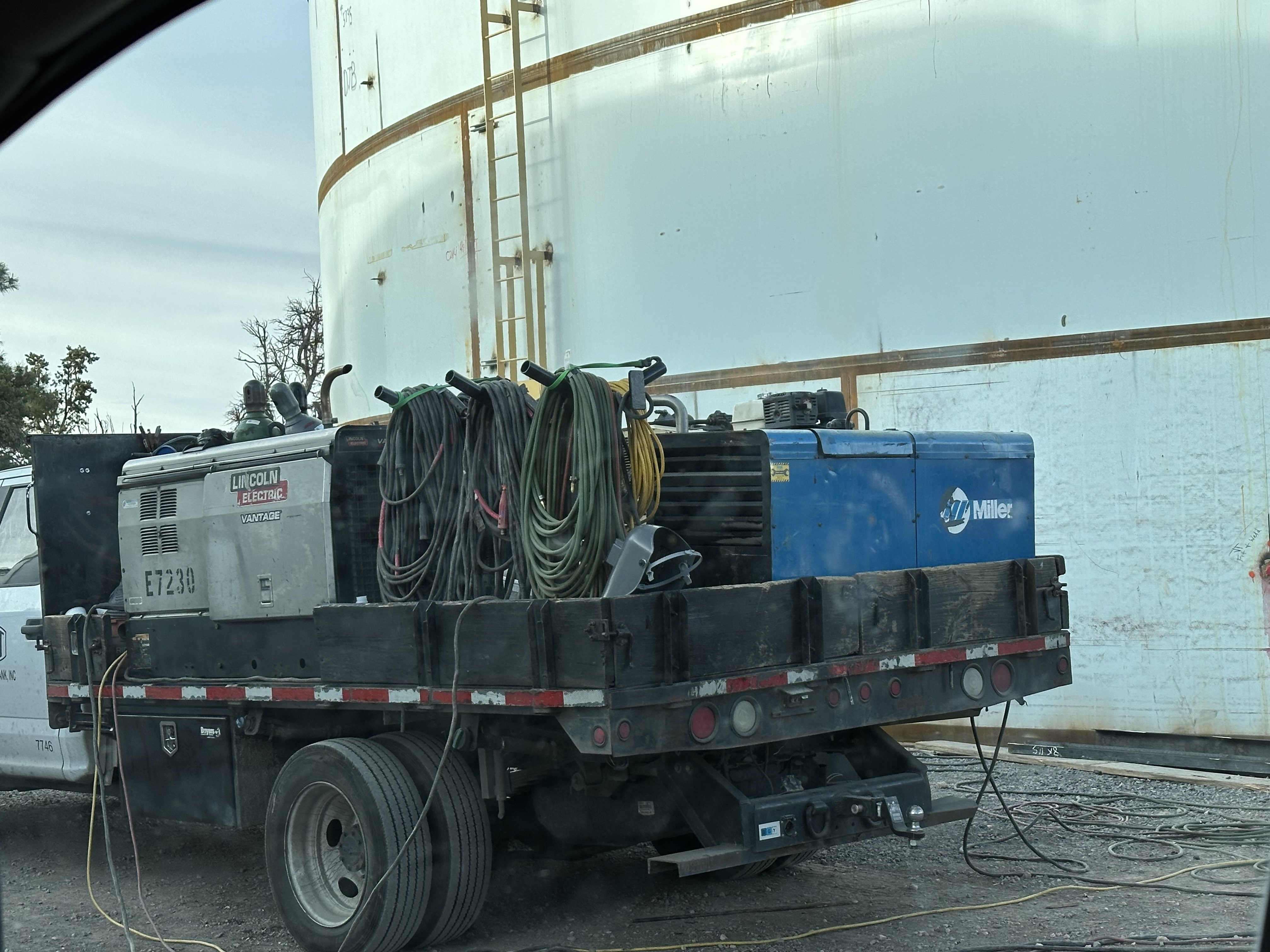
Normal inspections play a pivotal role in making certain compliance by determining prospective failings or deviations from recommended requirements. Examiners are trained to examine weld top quality, confirm product specs, and analyze the general structural stability of storage tanks. Their competence is important in making certain that welding processes fulfill the required security standards.
Furthermore, compliance with security requirements not just safeguards employees but likewise safeguards the setting from potential risks such as leakages or catastrophic failings. Organizations that focus on safety and security compliance are much better positioned to reduce dangers, boost functional performance, and foster a culture like it of safety and security within their labor force. In summary, keeping rigorous compliance with safety requirements is indispensable for the successful operation of container welding tasks in commercial setups.
Benefits of Normal Assessments
Normal assessments are important to preserving the architectural honesty and security of welded tanks. These inspections supply a methodical approach to recognizing prospective problems or weak points in the welds, making sure that any issues are resolved prior to they escalate right into significant failings. By carrying out routine analyses, organizations can identify rust, fatigue, and other forms of wear and tear that may compromise tank efficiency.
Furthermore, consistent assessments add to conformity with market policies and standards. Following these guidelines not just reduces legal risks yet likewise boosts the company's track record for safety and security and dependability. Routine evaluations cultivate a proactive security society, urging staff members to recognize and prioritize the value of tools integrity.

Situation Researches and Real-World Applications
Case researches and real-world applications highlight the tangible impact of effective container welding assessment practices. One remarkable example is a big petrochemical center that faced substantial operational disturbances due to leakages in storage containers. Complying with the application of extensive welding examination protocols, consisting of visual and ultrasonic screening, the facility determined crucial imperfections in weld seams that might have resulted in devastating failures. This proactive method not only stopped ecological dangers yet likewise saved the firm millions in potential clean-up prices and regulative penalties.
Likewise, a water treatment plant executed pop over to these guys a comprehensive examination program for its container welding operations - Tank Welding Inspection. By including non-destructive testing techniques, the plant was able to spot very early indications of rust and tiredness in weld joints. This prompt treatment prolonged the lifespan of the storage tanks and ensured conformity with safety and security guidelines, thus securing public health
These study highlight the significance of normal and systematic container welding assessments. By prioritizing these techniques, industries can mitigate threats, boost architectural honesty, and make sure conformity with safety requirements, ultimately leading to boosted functional performance and reduced responsibilities.

Conclusion
In verdict, container welding inspection is a vital part of preserving structural integrity and safety in commercial applications. Employing numerous assessment strategies ensures early discovery of possible problems, consequently protecting against tragic failures. Adherence to safety and security standards even more improves operational reliability and compliance with regulatory requirements. Ultimately, normal assessments not only shield public health and the environment but also add to the durability and effectiveness of important properties, underscoring the essential role of this practice in commercial operations.
Report this page